In recent years, with the increasing global emphasis on environmental protection and carbon emissions reduction, the European Union has introduced a new carbon tariff regulation. This regulation has significant implications for watch export enterprises, as it requires them to build a compliant supply chain to avoid potential high – cost carbon tariffs. This article will comprehensively analyze the new European carbon tariff regulations, propose detailed compliant supply chain building solutions, and elaborate on relevant service items and costs.
Contact us now
we are a licensed and trusted international trading company with years of experience in sourcing and fulfilling orders in China. Whether you’re looking for bulk purchases, customized products, or tailored logistics solutions, our team is dedicated to delivering transparent, reliable service.
📱 Contact Us on WhatsApp
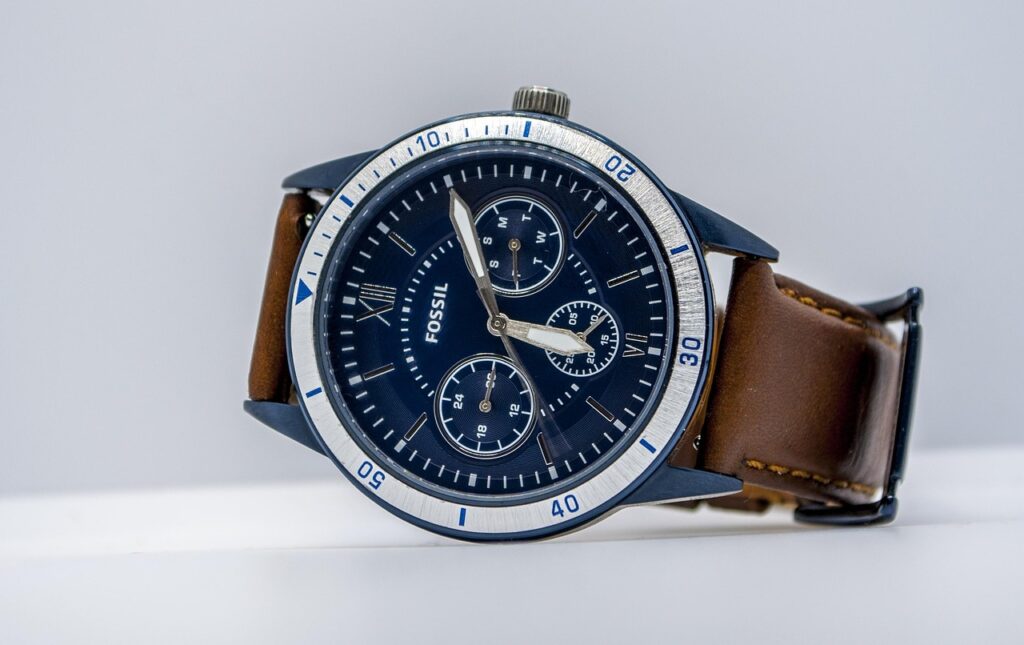
I. Analysis of the New European Carbon Tariff Regulations
A. Background and Purpose
The European Union’s carbon tariff regulation is part of its broader strategy to achieve carbon neutrality. The main purpose is to prevent carbon leakage, which occurs when companies relocate production to regions with less strict environmental regulations to avoid high carbon costs. By imposing a carbon tariff on imported goods, the EU aims to level the playing field between domestic and imported products in terms of carbon costs.
B. Key Provisions
- Carbon Emission Calculation: The regulation requires accurate calculation of the carbon emissions associated with the production, transportation, and distribution of products. For watch export enterprises, this means tracking the carbon footprint from the extraction of raw materials such as metals and precious stones to the final assembly of the watch.
- Reporting Requirements: Enterprises must report their carbon emissions data regularly. This includes detailed information about the sources of emissions, the methods used for calculation, and any measures taken to reduce emissions. Failure to report accurately or on time may result in penalties.
- Tariff Imposition: Based on the calculated carbon emissions, a carbon tariff will be imposed on imported products. The tariff rate is expected to increase gradually over time, creating a strong incentive for enterprises to reduce their carbon footprint.
II. Impact on Watch Export Enterprises
A. Cost Increase
Watch production involves multiple stages, from sourcing raw materials to manufacturing and shipping. Each stage contributes to carbon emissions. Under the new regulation, enterprises may face higher costs due to the carbon tariff, which could erode their profit margins. For example, if the carbon emissions associated with a batch of watches are high, the tariff could significantly increase the cost of exporting these watches to the EU.
B. Market Access Challenges
Non – compliance with the carbon tariff regulation may lead to restricted market access in the EU. As the EU is a major market for watch exports, any barriers to entry can have a significant impact on the business of watch export enterprises. Consumers in the EU are also becoming more environmentally conscious, and products with a high carbon footprint may face reduced demand.
III. Compliant Supply Chain Building Solutions
A. Raw Material Sourcing
- Selecting Low – Carbon Suppliers: Watch export enterprises should prioritize suppliers who use low – carbon production methods. For example, when sourcing metals, choose suppliers that have adopted advanced smelting technologies with lower energy consumption and carbon emissions.
- Service Item: Supplier screening and evaluation service. Professional agencies can help enterprises identify and assess potential raw material suppliers based on their carbon emissions records and environmental management systems.
- Cost: The cost of this service usually ranges from \(10,000 to \)50,000, depending on the complexity of the supply chain and the number of suppliers to be evaluated. This includes the cost of data collection, analysis, and on – site inspections if necessary.
- Sustainable Sourcing of Precious Stones: For watches that use precious stones, ensure that the stones are sourced from mines with sustainable mining practices. This not only helps reduce carbon emissions but also addresses ethical and environmental concerns.
- Service Item: Sustainable sourcing consulting service. Consultants can provide guidance on finding and verifying sustainable precious stone suppliers, as well as helping enterprises develop sustainable sourcing policies.
- Cost: Consulting fees for sustainable sourcing typically range from \(5,000 to \)30,000. This includes the cost of research, policy development, and initial supplier verification.
B. Production Process Optimization
- Energy – Efficient Manufacturing: Upgrade manufacturing equipment and processes to be more energy – efficient. For example, use energy – saving machinery in watch assembly, and optimize the layout of the production line to reduce energy waste.
- Service Item: Energy – efficiency improvement consulting and implementation service. Energy – efficiency experts can conduct an audit of the production process, recommend suitable equipment upgrades, and oversee the implementation of energy – saving measures.
- Cost: The cost of an energy – efficiency audit is usually around \(10,000 to \)20,000. Equipment upgrades can be more expensive, with costs ranging from $50,000 to several hundred thousand dollars, depending on the scale of the enterprise and the complexity of the upgrades.
- Waste Reduction and Recycling: Implement waste reduction and recycling programs in the production process. Recycle materials such as metal scraps and packaging waste, and reduce the use of non – recyclable materials.
- Service Item: Waste management consulting and implementation service. Consultants can help enterprises design waste reduction and recycling strategies, and connect them with reliable recycling partners.
- Cost: Waste management consulting fees are generally in the range of \(5,000 to \)20,000. The cost of setting up recycling facilities or outsourcing recycling services depends on the volume of waste and the complexity of the recycling process, and can range from \(10,000 to \)50,000 per year.
C. Transportation and Logistics
- Low – Carbon Shipping Options: Choose shipping methods with lower carbon emissions. For long – distance transportation to the EU, consider using sea freight with vessels that have relatively low emissions or are powered by alternative fuels. For domestic transportation within the EU, explore the use of electric or hybrid trucks.
- Service Item: Logistics carbon footprint analysis and optimization service. Logistics service providers can analyze the carbon emissions of different transportation routes and modes, and recommend the most carbon – efficient options.
- Cost: The cost of logistics carbon footprint analysis is usually around \(5,000 to \)15,000. The additional cost of using low – carbon transportation options may vary. For example, using a more fuel – efficient sea freight vessel may increase the shipping cost by 5% – 15%, while using electric trucks for domestic transportation may require an initial investment in vehicle procurement or leasing, which can range from \(20,000 to \)100,000 per vehicle.
- Supply Chain Visibility and Optimization: Implement a supply chain management system that provides real – time visibility of the movement of goods. This helps in optimizing transportation routes, reducing unnecessary detours, and minimizing carbon emissions.
- Service Item: Supply chain management system implementation service. Technology companies can help enterprises select and implement a suitable supply chain management system, and provide training and support.
- Cost: The cost of implementing a supply chain management system can range from \(30,000 to \)100,000, depending on the size of the enterprise and the complexity of the system. This includes software licensing fees, implementation costs, and training expenses.
D. Carbon Emission Accounting and Reporting
- Accurate Carbon Emission Calculation: Use reliable carbon accounting methods and tools to calculate the carbon emissions associated with the entire supply chain. This requires collecting data on energy consumption, transportation distances, and raw material extraction processes.
- Service Item: Carbon accounting service. Professional carbon accounting firms can help enterprises establish accurate carbon accounting methods, collect relevant data, and calculate carbon emissions.
- Cost: Carbon accounting services typically charge between \(10,000 and \)50,000 per year, depending on the complexity of the supply chain and the frequency of reporting.
- Compliant Reporting: Ensure that all carbon emissions data is reported accurately and in a timely manner in accordance with the EU’s requirements. This may involve preparing detailed reports and submitting them through the appropriate channels.
- Service Item: Carbon reporting consulting and submission service. Consultants can assist enterprises in preparing carbon reports that meet EU standards and submit them on behalf of the enterprise.
- Cost: The cost of carbon reporting consulting and submission services is generally around \(5,000 to \)20,000 per reporting period.
IV. Case Studies
A. Case of Company A
Company A is a medium – sized watch export enterprise. After learning about the new European carbon tariff regulations, it decided to take action. It hired a supplier screening agency to evaluate its raw material suppliers. The cost of this service was \(20,000. Based on the agency’s recommendations, it switched to a low – carbon metal supplier, which increased the cost of raw materials by about 8% but reduced the overall carbon emissions of the product. In the production process, Company A invested \)80,000 in energy – efficiency upgrades, including installing energy – saving lighting and upgrading some manufacturing equipment. It also implemented a waste reduction and recycling program, with an initial investment of \(15,000. For transportation, it worked with a logistics service provider to analyze its carbon footprint. The analysis cost \)8,000, and as a result, it switched to a more fuel – efficient sea freight carrier, which increased the shipping cost by 10%.
In terms of carbon accounting and reporting, Company A hired a carbon accounting firm at a cost of \(25,000 per year and a reporting consultant for \)10,000 per reporting period. After implementing these measures, Company A was able to reduce its carbon emissions by 30% and was well – prepared to comply with the European carbon tariff regulations.
B. Case of Company B
Company B, a large – scale watch export enterprise, took a more comprehensive approach. It established an in – house sustainability team to manage its supply chain’s carbon footprint. The annual cost of maintaining this team, including salaries and related expenses, was approximately \(200,000. The company also invested \)300,000 in research and development to develop new manufacturing processes with lower carbon emissions. It sourced its precious stones from mines certified for sustainable mining, with an additional cost of about 15% for the stones.
For transportation, Company B developed its own supply chain management system at a cost of \(80,000 to optimize transportation routes. It also introduced a fleet of electric trucks for domestic transportation in the EU, with an investment of \)500,000 for vehicle procurement.
In carbon accounting and reporting, Company B used a combination of in – house resources and external consulting. The annual cost of carbon accounting was about \(30,000, and the cost of reporting consulting was \)15,000 per reporting period. As a result, Company B was able to reduce its carbon emissions by 40% and was seen as a leader in sustainable supply chain management in the watch industry.
V. Conclusion
Under the new European carbon tariff regulations, watch export enterprises need to take proactive measures to build a compliant supply chain. By optimizing raw material sourcing, production processes, transportation and logistics, and carbon emission accounting and reporting, enterprises can reduce their carbon footprint, meet regulatory requirements, and maintain their competitiveness in the European market. Although implementing these solutions requires certain investments, the long – term benefits in terms of cost savings, market access, and brand image are significant. As the global focus on carbon emissions reduction continues to grow, watch export enterprises that adapt early to these changes will be better positioned for success.
Tags:European carbon tariff, watch export enterprises, compliant supply chain, carbon emissions, supply chain optimization, cost management