1. Introduction
In the contemporary global market, the watch industry is constantly evolving to meet the ever – changing demands of consumers. With the advent of “Industry 4.0”, which is characterized by the integration of digital technologies, automation, and data – driven decision – making, watch manufacturers are presented with new opportunities and challenges. One of the significant developments within this framework is the implementation of flexible production lines, which can support orders starting from 10,000 pieces. This article will explore the “Industry 4.0” upgrade in the watch industry, focusing on the features, service items, and costs associated with these flexible production lines.
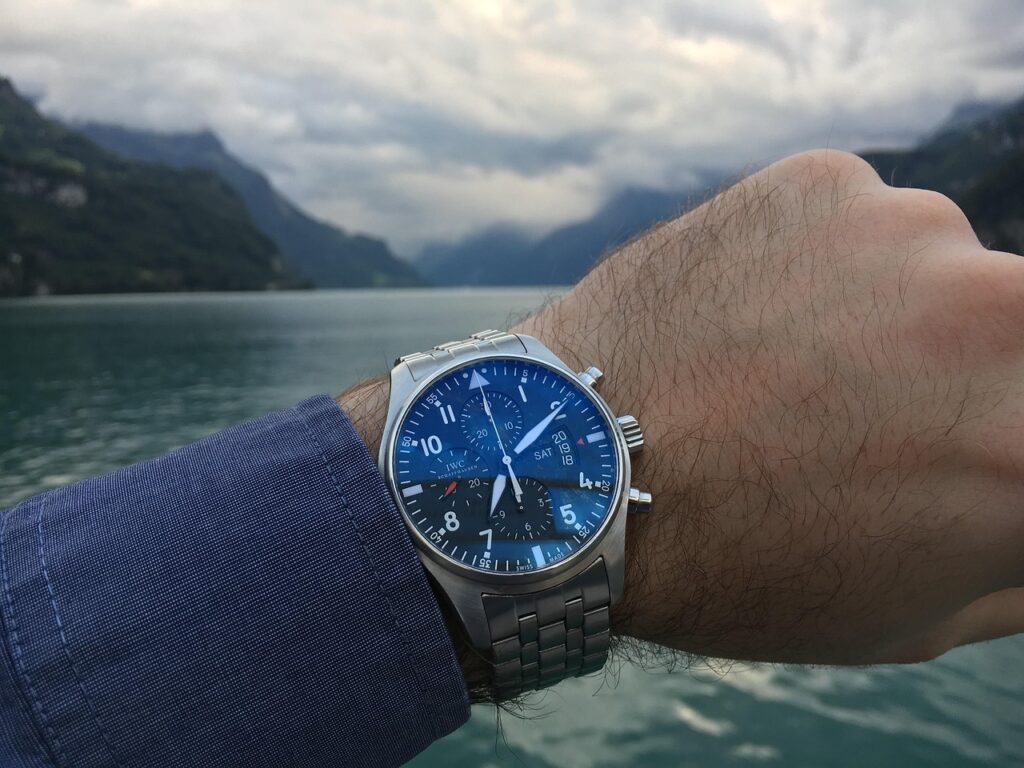
2. The Background and Significance of “Industry 4.0” in the Watch Industry
2.1 Changing Consumer Demands
- Increasing Personalization: Modern consumers, especially the younger generations, are more inclined towards personalized products. They seek watches that not only tell time but also reflect their individual style, preferences, and even values. For example, some consumers may want a watch with a unique dial design that incorporates their favorite color or a symbol that holds personal significance. Traditional mass – production models struggle to meet such personalized demands efficiently.
- Shorter Product Life Cycles: The fashion and technology industries are highly dynamic, and the watch industry is no exception. New watch models are introduced more frequently, and the lifespan of a particular model has significantly decreased. This means that watch manufacturers need to be able to quickly adapt to these changes and produce new products in a timely manner.
2.2 The Need for Efficiency and Cost – Effectiveness
- Cost – Reduction Pressures: In a highly competitive global market, watch manufacturers face intense cost – reduction pressures. Traditional production methods often involve high setup costs for each new product line, long production lead times, and significant inventory holding costs. By embracing “Industry 4.0” and its flexible production lines, manufacturers can optimize their production processes, reduce waste, and improve overall efficiency.
- Improving Productivity: The integration of advanced technologies such as the Internet of Things (IoT), artificial intelligence (AI), and robotics in the production process can significantly enhance productivity. For instance, robots can perform repetitive tasks with high precision and speed, reducing the risk of human error and increasing the output per unit of time.
3. Understanding Flexible Production Lines in the Watch Industry
3.1 Key Features of Flexible Production Lines
- Modular Design: Flexible production lines in the watch industry are designed with modular components. This means that different parts of the production process, such as movement assembly, case manufacturing, and dial printing, can be easily reconfigured or replaced. For example, if a manufacturer wants to start producing a new type of watch movement, they can simply swap out the relevant modules on the production line rather than overhauling the entire production system.
- Automation and Robotics: These production lines rely heavily on automation and robotics. Robots can be programmed to perform tasks such as picking and placing components, soldering, and quality inspection. For example, in the assembly of watch movements, robots can precisely insert tiny gears and springs, ensuring consistent quality. The use of automation also reduces the need for a large manual labor force, which can be both costly and subject to human error.
- Digital Integration and Data Analytics: Flexible production lines are integrated with digital systems. Sensors are installed throughout the production process to collect data on various parameters such as production speed, component quality, and machine performance. This data is then analyzed in real – time using AI algorithms. For example, if the data indicates that a particular machine is starting to produce components with a higher defect rate, the system can automatically adjust the machine settings or schedule maintenance to prevent further issues.
3.2 Advantages of Flexible Production Lines
- Quick Adaptability to Order Changes: With a flexible production line, watch manufacturers can quickly adjust to changes in order volume, product design, or delivery schedules. For example, if a customer suddenly increases their order quantity from 10,000 to 15,000 pieces, the production line can be easily reprogrammed to increase the production rate without significant disruptions. Similarly, if a new design requirement is introduced, the modular components of the production line can be reconfigured to accommodate the change.
- Reduced Production Costs: The use of automation and data – driven optimization reduces waste, minimizes setup times, and improves overall production efficiency. For example, by using AI – powered quality control systems, manufacturers can identify and reject defective components early in the production process, reducing the cost of rework and waste. Additionally, the ability to quickly change production runs without extensive setup reduces the overall cost per unit.
- Enhanced Product Quality: Robots and automated systems perform tasks with high precision, resulting in a more consistent product quality. For example, in the engraving of watch cases, a robotic engraving machine can create intricate patterns with a higher level of accuracy compared to manual engraving. The real – time data analysis also allows for continuous improvement in the production process, further enhancing product quality.
4. Service Items Provided by Flexible Production Lines in the Watch Industry
4.1 Production Planning and Scheduling
- Order Management: Manufacturers with flexible production lines offer comprehensive order management services. They work closely with clients to understand their order requirements, including the quantity, product specifications, and delivery deadlines. The production team then creates a detailed production plan that optimizes the use of the production line resources. For example, if a client has an urgent order, the production schedule can be adjusted to prioritize that order while still ensuring the efficient use of the production line. The cost of order management services is typically included in the overall production cost, but for complex orders with multiple changes and tight deadlines, an additional fee of 5% – 10% of the total production cost may be charged.
- Production Scheduling Optimization: Using advanced scheduling software and data analytics, manufacturers can optimize the production schedule to minimize downtime and maximize productivity. The software takes into account factors such as machine availability, component inventory levels, and production lead times. For example, it can schedule the production of different watch models in a sequence that reduces the need for frequent reconfiguration of the production line. The cost of developing and maintaining this scheduling software is absorbed by the manufacturer, but clients may see the benefits in the form of faster production times and lower costs.
4.2 Customization Services
- Design Customization: Flexible production lines enable a high degree of design customization. Manufacturers can work with clients to create unique watch designs, from the dial and case design to the choice of materials and finishes. For example, a client may want a watch with a wooden case or a dial made of recycled materials. The design team will collaborate with the client to develop a design concept and then translate it into a production – ready design. The cost of design customization depends on the complexity of the design. Simple design changes, such as changing the color of the dial, may cost an additional \(5 – \)20 per unit, while more complex customizations, such as creating a completely new case design, can cost \(50 – \)200 per unit.
- Component Customization: In addition to design customization, manufacturers can also offer component customization. This includes custom – made watch movements, straps, and clasps. For example, a client may request a watch movement with a specific power reserve or a strap made of a rare type of leather. The cost of component customization varies widely depending on the component and the level of customization. A custom – made watch movement can cost anywhere from \(500 – \)5,000 extra per unit, while a high – end custom leather strap may add \(100 – \)500 to the cost per unit.
4.3 Quality Control and Assurance
- In – Line Quality Monitoring: Flexible production lines are equipped with advanced quality monitoring systems. Sensors and cameras are used to monitor the production process in real – time, checking for defects in components, incorrect assembly, and other quality issues. For example, in the watch movement assembly process, sensors can detect if a gear is not properly aligned. The cost of implementing and maintaining these in – line quality monitoring systems is significant, but it helps to reduce the number of defective products. The cost of quality control is typically 3% – 5% of the total production cost.
- Final Inspection and Certification: After the production process is complete, each watch undergoes a final inspection. This includes checking the timekeeping accuracy, the functionality of all features, and the overall aesthetic appearance. Watches that pass the inspection are then certified. The cost of final inspection and certification is also included in the overall quality control cost. For watches that require additional certifications, such as water – resistance certification for diving watches, an additional fee of \(10 – \)50 per unit may be charged.
4.4 Logistics and Delivery
- Inventory Management: Manufacturers with flexible production lines can also offer inventory management services. They can store finished products on behalf of clients and manage the inventory levels based on the client’s sales forecasts. For example, if a client expects a spike in sales during a particular season, the manufacturer can adjust the inventory levels accordingly. The cost of inventory management services is usually charged as a percentage of the value of the inventory stored, typically 2% – 5% per month.
- Delivery and Shipping: Manufacturers are responsible for arranging the delivery of the finished products to the client. They can work with various shipping partners to ensure timely and secure delivery. The cost of shipping depends on factors such as the quantity of products, the destination, and the shipping method. For example, shipping a batch of 10,000 watches from China to the United States by sea may cost \(1,000 – \)3,000, while air freight may cost \(5,000 – \)10,000.
5. Cost Analysis of Flexible Production Lines in the Watch Industry
5.1 Initial Investment Costs
- Equipment and Technology Adoption: The implementation of flexible production lines requires a significant initial investment in equipment and technology. This includes the purchase of robots, automated machinery, sensors, and software systems. For example, a state – of – the – art robotic assembly system for watch movements can cost upwards of \(500,000, while the software for production scheduling and data analytics may cost \)100,000 – $500,000. The cost of integrating these systems and ensuring their compatibility can also be substantial, often adding another 10% – 20% to the equipment cost.
- Factory Renovation and Infrastructure Upgrades: In many cases, manufacturers need to renovate their factories to accommodate the new production lines. This may involve modifying the layout of the factory floor, upgrading the electrical and mechanical infrastructure, and installing climate – control systems to ensure optimal conditions for the production equipment. The cost of factory renovation can range from \(200,000 to over \)1 million, depending on the size of the factory and the extent of the upgrades.
5.2 Operational Costs
- Labor Costs: Although flexible production lines rely heavily on automation, there is still a need for skilled labor. Workers are required to operate, maintain, and program the automated systems. The cost of labor for a production line that can handle orders starting from 10,000 pieces may include salaries for machine operators, technicians, and quality control personnel. On average, the annual labor cost for a team of 10 – 15 skilled workers can range from \(500,000 to \)1 million.
- Maintenance and Repairs: The automated equipment on the production line requires regular maintenance to ensure its optimal performance. This includes preventive maintenance, such as lubrication, calibration, and replacement of worn – out parts. In case of breakdowns, repairs need to be carried out promptly to minimize production downtime. The cost of maintenance and repairs can be significant, with an annual budget of \(50,000 – \)200,000 for a typical flexible production line.
- Energy Costs: The operation of automated machinery, sensors, and data – processing systems consumes a significant amount of energy. The energy cost for running a flexible production line can range from \(30,000 to \)100,000 per year, depending on the size of the production line and the energy – efficiency of the equipment.
5.3 Cost – Savings and Return on Investment
- Cost – Savings in the Long Run: Despite the high initial investment and operational costs, flexible production lines can lead to significant cost – savings in the long run. The reduction in waste, the ability to quickly adapt to order changes, and the improvement in production efficiency can lower the cost per unit. For example, by reducing the defect rate from 5% to 1% through better quality control, a manufacturer can save a substantial amount in rework and waste costs. Over a period of 3 – 5 years, the cost – savings can offset the initial investment and start generating a positive return on investment.
- Increased Profit Margins: The ability to offer customization services and meet the changing demands of consumers can also lead to increased profit margins. Custom – made watches often command a higher price, and the efficient production process allows manufacturers to capture a larger share of the market. For example, if a manufacturer can increase the price of a watch by 20% due to customization and reduce the production cost by 10% through improved efficiency, the profit margin can increase significantly.
6. Case Study: A Watch Manufacturer’s Success with Flexible Production Lines
XYZ Watch Manufacturer, a mid – sized company in Switzerland, decided to upgrade to a flexible production line as part of its “Industry 4.0” initiative. The initial investment in equipment, technology, and factory renovation was approximately \(2 million. However, within the first year of operation, they were able to achieve a 30% reduction in production costs due to increased efficiency and reduced waste. The company started receiving more orders due to its ability to offer customization services. For example, a luxury brand ordered 15,000 custom – made watches with unique dial designs and high – end materials. The customization service added an average of \)100 per unit to the cost, but the selling price of these watches was $300 higher than their standard models.
In terms of quality control, the in – line monitoring system reduced the defect rate from 4% to 1.5%, resulting in significant savings in rework costs. The company also optimized its logistics and delivery services, reducing the delivery time by 20% and improving customer satisfaction. Overall, XYZ Watch Manufacturer saw a 50% increase in profit within two years of implementing the flexible production line, demonstrating the effectiveness of this “Industry 4.0” upgrade.
7. Conclusion
The “Industry 4.0” upgrade in the watch industry, particularly the implementation of flexible production lines that support orders starting from 10,000 pieces, offers numerous benefits to watch manufacturers. By understanding the key features and advantages of these production lines, as well as the service items they provide and the associated costs, manufacturers can make informed decisions about adopting this technology. The ability to adapt to changing consumer demands, improve production efficiency, and offer customization services can give watch manufacturers a competitive edge in the global market. While the initial investment and operational costs are significant, the long – term cost – savings and increased profit margins make it a worthwhile investment. With careful planning and execution, the “Industry 4.0” upgrade can transform the watch industry and open up new opportunities for growth and innovation.
Tags
Watch industry,Industry 4.0,Flexible production lines,Customization services,Cost analysis,Manufacturing technology
Why choose us?
- Competitive wholesale prices: We offer discounted rates based on purchase quantity (minimum order quantities apply).
- Quality assurance: All products are inspected and certified to meet international standards.
- Flexible payment terms: Secure transactions with T/T, L/C, or Alipay.
For detailed pricing, simply click the contact button in the bottom right corner to request a tailored quote!
📱 Contact Us on WhatsApp